The Essential Guide to Plastics Injection Molding Companies
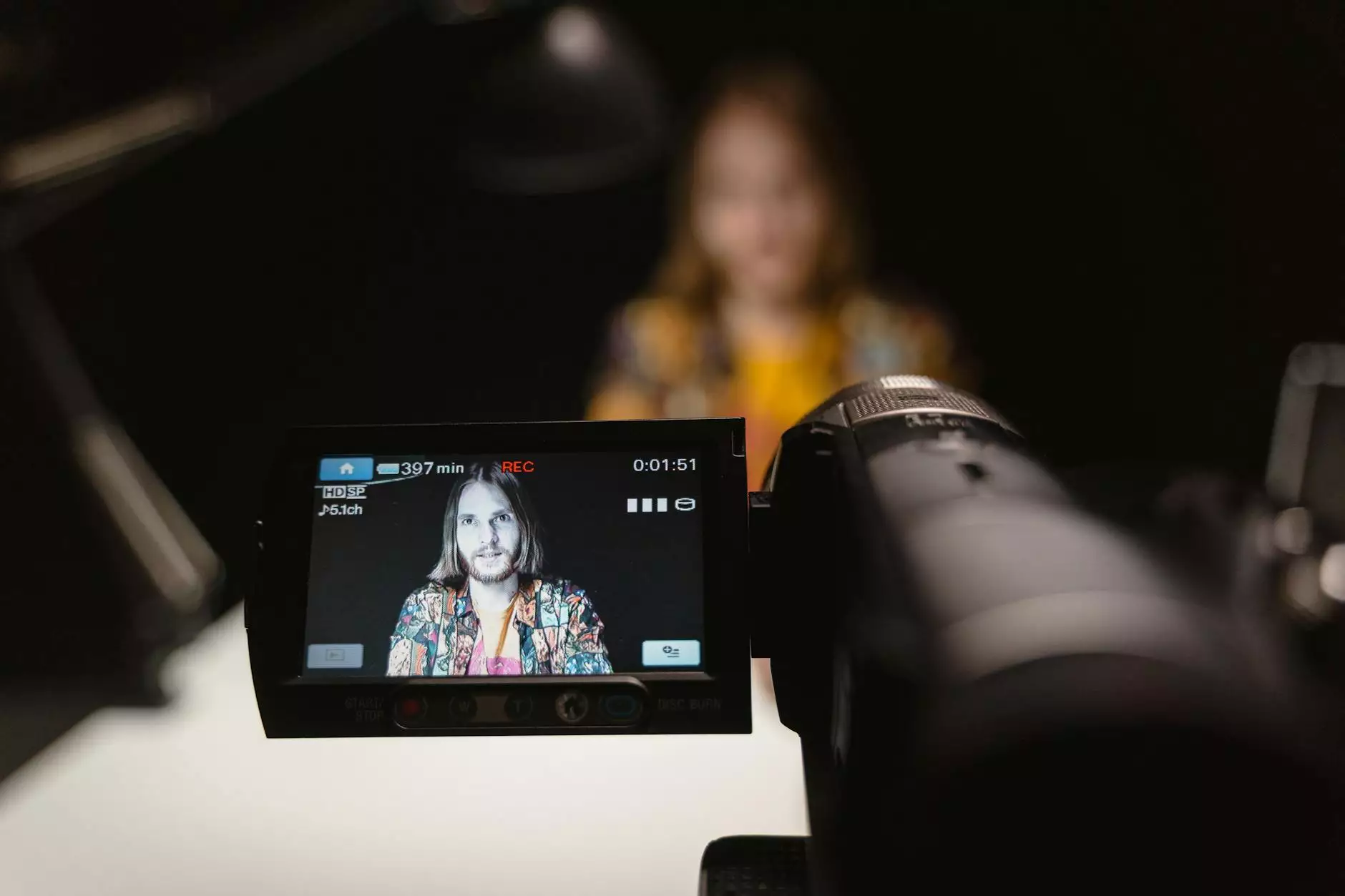
The manufacturing landscape is continuously evolving, and one of the pivotal technologies driving this change is plastics injection molding. This technique is utilized by numerous plastics injection molding companies, playing a significant role in shaping modern products across various industries.
Understanding Plastics Injection Molding
Plastics injection molding is a manufacturing process wherein plastic material is heated until it melts and then injected into a mold. Once cooled and solidified, the mold is opened, yielding a precise and consistent product. This method is favored for its ability to produce large volumes of high-quality components with minimal waste.
The Process of Injection Molding
Here’s a breakdown of the key stages in the injection molding process:
- Material Selection: The process begins with selecting suitable plastic materials, typically polymers, which can include thermoplastics and thermosetting plastics.
- Melt Preparation: The chosen material is fed into a heated barrel, where it is melted and maintained at a specific temperature to ensure optimal flow characteristics.
- Injection: The molten plastic is injected into a mold cavity using a screw or plunger mechanism under high pressure.
- Cooling: The injected material begins to cool and solidify within the mold, assuming its desired shape.
- Mold Opening and Ejection: Once the product has cooled sufficiently, the mold opens, and the finished component is ejected.
- Post-Processing: This may include trimming, finishing, and assembly of components as required.
Benefits of Using Plastics Injection Molding Companies
Choosing to work with established plastics injection molding companies offers numerous advantages that can enhance both production efficiency and product quality. Here are some key benefits:
- Cost Efficiency: Mass production leads to lower per-unit costs, making it an economical choice for manufacturers.
- High Precision: Injection molding provides exceptional accuracy and repeatability, ensuring that each piece meets strict specifications.
- Material Versatility: A wide variety of plastics can be molded, each with unique properties suitable for different applications.
- Reduced Waste: With precise measurements and automated processes, waste is minimized compared to traditional manufacturing methods.
- Innovation in Design: Advanced molding techniques allow for intricate designs that were previously impossible to achieve with older methods.
Industries Benefiting from Injection Molding
Plastics injection molding companies cater to an extensive array of industries. Here’s a closer look at some sectors that leverage this technology:
1. Automotive Industry
The automotive industry relies heavily on injection molding for producing interior components like dashboards, buttons, and covers. These parts often require high durability and a precise fit, provided reliably by injection molding.
2. Consumer Electronics
In consumer electronics, countless parts, from casing to intricate connectors, are produced using injection molding. This ensures high-quality finishes and performance reliability.
3. Medical Devices
The medical industry utilizes injection molding to create components that meet stringent regulatory standards. Items like syringes, housing for devices, and even components of diagnostic equipment are produced using this technology.
4. Packaging
Plastic packaging for food, beverages, and pharmaceuticals takes advantage of injection molding. Companies benefit from its ability to produce lightweight, cost-effective, and versatile packaging solutions.
Factors to Consider When Choosing Plastics Injection Molding Companies
Selecting the right plastics injection molding companies is crucial for the success of your projects. Here are important factors to weigh during your search:
- Experience and Expertise: Companies with a proven track record in the industry tend to offer better reliability and advice.
- Technology and Equipment: Latest injection molding machines and technologies can enhance efficiency and accuracy.
- Quality Assurance Processes: Look for companies that have robust quality control measures to ensure product consistency.
- Customization Options: The ability to customize molds and processes can provide tailored solutions that best meet your needs.
- Customer Service and Support: Effective communication and support are vital to address any concerns or changes during the process.
The Future of Plastics Injection Molding
As industries evolve, so does the technology and approach of plastics injection molding companies. The future looks bright, with trends pushing for:
- Sustainability: Increasing pressure to utilize recycled materials and reduce waste is prompting innovations in sustainable practices.
- Smart Manufacturing: Automation, IoT, and AI technologies are changing how injection molding operations are managed, leading to increased efficiency.
- Advanced Materials: Development of new polymer materials and composites offers greater flexibility in design and performance.
- Customization and Shorter Production Times: Companies are leaning towards systems that allow for quicker changeovers and production runs.
Conclusion
In summary, plastics injection molding companies play a pivotal role in modern manufacturing, providing remarkable efficiency and precision across various sectors. With the continual advancements in technology and a growing focus on sustainability, the landscape of injection molding is set to become even more dynamic. Partnering with the right injection molding company can pave the way for innovations in product design and manufacturing processes, ultimately enhancing your business's competitiveness in the market.
As you evaluate your options, consider the benefits of working with experienced and technologically advanced plastics injection molding companies like DeepMould.net, which cater to your specific needs while ensuring top-quality outcomes.